ものづくりに関する記事を書いてきました
その一部です
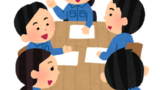
書いている私自身、現役のサラリーマンとして海外の製造会社の経営しながら実践しています
今回、記事に書いてきたような考えをどのような経験をもとに自分の中で構築し、実践してきたか、自分の仕事を振り返ってみたいと思います
前回の記事で、初めて海外製造工場に赴任し生産現場の改善活動を始めるところまでお話ししました
今回は、最初の拠点で製造現場の改善活動をする中で学んできたことです
下記は、ものづくりに関するプロフィールです。参考まで
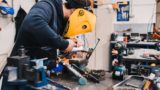
私のこれまでのものづくりに関する記事は下記の観点で書いてきました
①開発が意識するべきこと
②工場の生産性を上げる
③多様性を受け入れる
④現場力強化
このうち ①の開発に関する記事は、海外赴任する前、開発業務にかかわりながら自分で考えてきたことが中心です
②③④については、海外製造会社に赴任してからの経験から学び、自分なりに到達した結論をまとめたものです
最初の海外製造会社で現場改善を始める
中国の工場の先輩の意見を聞いて、まずは製造現場の改善をすることから始めました
製造は工場として付加価値を生み出す部門である
工場のQCDのレベルアップが会社の収益化につながる
そんな思いからでしょうか
QCDと言っても、最初はC=生産性しか考えいなかったと思います
さて、さて現場改善と言っても私自身は製造の経験は全くありません
ローカルの工場長と話しても
「毎月の決められた生産数量を生産する」
との考えで、そこに「効率的に」という概念はありませんでした
なので、まずは「月単位の生産数量」ではなく「時間、人当たりの生産台数もしくは生産額」をKPIにすることを提案しました
なんとなく理解したみたいですが、私自身の経験、知見不足もありなかなかうまく進みませんでした
そこで、またまた中国にいる先輩に相談し、本社にいる現場改善のチームを紹介してもらうことになりました
これが、私にとってモノづくり(工場)の基本を勉強する大きな切っ掛けになったことは間違いありません
その後の製造工場の経営を任されるにおいて非常に大きなターニングポイントの一つだったと思います
現場改善指導を受ける
本社の改善チームにお願いして、自分の担当会社に指導員を派遣してもらいました
毎月1週間程度滞在し、現場でローカルと一緒にとことん会話しながら改善の仕方を教えるスタイルです
余談ですが、この指導員は私が寮生活をしていた時の後輩でした
メッチャ生意気なやつでしたが、ものづくりに対する知見はすごかったです
トヨタ出身のコンサルの先生に入門し、かなり鍛えらえたようです
私も、先輩後輩の仲は抜きにして、徹底的にコイツから学ぼうと腹をくくって、指導に来るときは通常の仕事はせず、その指導員について従業員と一緒に学ぶことにしました
そこで学んだことが②工場の生産性を上げるに書かれています
最初の製造拠点で学んだこと
その寮の後輩である指導員から学んだことは数知れません
今までの記事に書いてきていますが、書ききれていないことも多いようです(反省)
今思えば当たり前ですが・・・
◇お客様と約束した納期通りの出荷
◇品質は何で保証するのか
◇在庫の意味
◇生産性を上げるための手法
などなど、数え切れません
簡単に説明してみます
◇お客様と約束した納期通りの出荷
当時私が担当した工場メンバーは月末になると、急に忙しそくなります
理由を聞くと「月内の生産計画数量を達成するため」
製造のことを全く知らなかった私は「そんなもんか・・・」くらいに聞いていたのですが、まず最初に指導員に思いっきり指摘されました
「生産するはいいのですが、納期通りに出荷してますか?」
全く答えられなかったですね
調べてみると、生産計画は出荷計画と連動していませんし、現場も出荷計画に生産を間に合わそうと考えている様子もない状態でした
月内に生産完了の帳尻を合わすために、必要なものでなく生産できるものを生産している状態でした
そりゃ、いかんですね
改善の第一歩でした
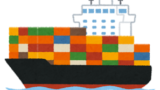
◇品質は何で保証するのか
これに対する考えも甘かったですね
商品開発の仕事をしてきたのですが、正直、答えることができませんでした
「開発完成度と図面通りの部品」
当時は、こんなレベルではなかったかな・・・
製造の現場に聞くと多いのが「検査」で保証
これも違います
答えは「正しい部品」「正しい道具」「正しい作業」+「正しい設計」
これも、当時「目から鱗」でした
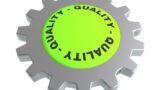
◇在庫の意味
当時、会社指示で「在庫を減らせ」とやたら言われていました
恥ずかしながらキャッシュリッチな工場で仕事をしていたので、お金に困ることもなく
「在庫?? 持てるだけ持ったらええんちゃう、部品切れんでええし」
「減らせ減らせ、うるさいのぉ」
信じられないくらいの未熟な認識で仕事してました
この指導員から学んだのが「適切な在庫を持て」
最初意味不明でした「適切な在庫ってなんやねん」
て感じです
言ってみれば「工場の能力に応じた最小の在庫」でしょうか
力のない工場は、在庫が少ないと工程が止まります
レベルの高い工場が極少の在庫で何の問題もなく生産できます
つまり在庫は工場の能力を測定するKPIと私は理解しています
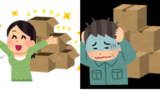
◇生産性を上げるための手法
私が工場の現場改善に着手した時、一番最初に考えた目的が「生産性」でした
いかに効率よく生産するか
これでコストが下がり、利益が増えると考えていたのですが、きわめて短絡的な、部分的しかものが見えていなかったと痛切に反省しています
「生産性の改善」はあくまで手段であり目的ではありません
お客様に納期通り、よい品質のものを届けるための一手段です
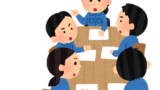
まとめ
最初に担当した製造会社の現場改善のために呼んだ指導者から学んだことのおさらいの記事なりました
学ぶことにかなりの時間を使いました
土曜日、指導員とバンコクの中華料理屋で5時間くらい大激論したこともいい思いです
(寮の後輩のクセに、生意気に上から目線で話す後輩にカチンときた私の未熟な面もあったことも一つです)🤣
しかしおかげで、ものづくりの基本的なところを学ぶことができたと思います
いま、私の周りの製造会社の社長さん見てると、製造出身の人はあまりないように見えます
大企業になるほどその傾向を感じます
そのため、社長がものづくりを知らずに経営し、現場に任せていることが気になります
私は、製造をじっくり学ぶ機会を得ることができ、運がよかったのかなと感じています
次回は、同じタイで学んだも一人の先生につていての話を書きたいと思います
コメント