ものづくりに関する記事を書いてきました
その一部です
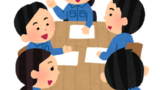
書いている私自身、現役のサラリーマンとして海外の製造会社の経営しながら実践しています
今回、記事に書いてきたような考えをどのような経験をもとに自分の中で構築し、実践してきたか、自分の仕事を振り返ってみたいと思います
今回はその1回目、最初の赴任直後までの話です
下記は、ものづくりに関するプロフィールです。参考まで
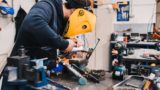
私の記事の観点
色々と記事を書いてきましたが、ものづくり関しては以下の観点で書いて書いています
①開発が意識するべきこと
②工場の生産性を上げる
③多様性を受け入れる
④現場力強化
ものづくりに限らない話もありますが、内容が製造会社中心なので「ものづくり」の範疇に入れています
あと、上記にカテゴライズできない内容は「ものづくりの話」として分けて書いています
上の①~④は自分の経験の中で「こうあるべき」とある程度考えが固まった内容
「モノづくりの話」は過去、および現在ものづくりの現場で感じたことを中心に書いています
(多少、その定義がクリアではない部分はりますがご容赦)
①~④に関して、今現役のサラリーマンとして海外製造会社の経営を任されている立場で、自分自身が実践しようと心掛けている内容です
今回、その考え方だどのように構築されたか書いてみました
製造会社経営の経験
いままでサラリーマンとして海外の4つ製造会社の経営を担当してきました
現在4社目です
我ながら、よくやってきたと思います
44歳の時に、初めて会社の経営を任されて14年間、多くのことを経験し学ぶことができました
最初から、今の考え方にたどりついたわけではなく、いろんな人からの教えや経験の中で培ってきました
その間、タイの大洪水や会社閉鎖も経験しています
(別記事参考にしてください「モノづくりの話」のカテゴリーに入れています)
これらトピック的なことからも多く学びましたが、やはり日常の経営のなかから学び考え実践してきた方が圧倒的に多いです
ですので、最初の頃ははっきりダメダメ経営者でした
「今が十分まとも」ということではありませんが、ブログ記事として残すくらいの知見を得ることができたとは思います
海外製造会社に赴任する前
44歳の時にタイに赴任し製造会社経営の責任者になる前は日本では商品開発の責任者でした
先の4つの観点の内①開発が意識するべきことは開発時代に自分なり構築していった考えを書いています
製造会社の経営をする前ですね
当然、私オリジナルの考えでなく、多くの先輩たちに教えてもらったことや、部門の歴史の中で築かれた文化、手法、制度をベースに私になりの考えも含めて、部下たちに語ってきたことを文書にしました
これらのことは、4つの製造会社にある開発部門に変わることなく語り続けてきました
ただ、最初のタイの会社以外どこまで定着したかは、自信がありません
DR等の場面でレビューしますが、会社のカルチャーとして根付くまではできていない感じがします
最初のタイの会社は、自分の出身部門の会社ですので、基本の考え方が共有化されているので比較的伝わりやすかったです
しかし、他の3つの会社は、全然経験のない事業でしたので、そこのメンバーは他の部門から来た私の言うことに抵抗があったように感じます
部門が変われば、考え方も方法も異なります
特に現地にいる日本人が・・
「今までの方法で何が悪いんねん・・」みたいな感じですね
こうなると、難しいですね
まだまだ修行が足りません
最初の製造会社(タイ)、手探りからのスタート
44歳の時にタイに赴任し始めての製造会社の経営を任されました
(ちなみに会社には工場だけでなく開発部門もあり商品開発を行っています)
振り返れば、当時、自分に自信たっぷりの私は、怖いもの知らずで工場の経営対して軽く考えていた面があったと思います
比較的高収益な事業を担当していましたし、その商品の開発の段階で利益がしっかり稼げる商品を開発してきたつもりがありました
はっきり言って「経営」について何も考えていなかった思います
「いい商品開発しとけば儲かる」この程度の考えだったかもしれません
さらに事業の「事業戦略」、「商品戦略」もある程度親元から出てきていましたし、その中で海外会社が果たすべき役割的なものをある程度クリアになっていたと思います
そして、その方向性に従って商品を「開発、製造すれば利益も出るんちゃうか」、みたいな感じです
完全に舐めていましたね
いざ経営してみると、利益に対する責任の重さに苦しめられることになります
ただ商品を開発して製造して売るだけでは利益なんか出ません(超当たり前です)
またQCDをレベル高くし商品を売ることの難しさに対する意識が超甘い
しかもPLしか見ることができず、BSやキャッシュフローも全然理解できていない恥ずかしい状況でした
「こりゃいかん!!、どないすりゃええねん」
誰も教えてくれません
従業員は約2000人
トップがしっかり方針を明確にしないと、皆が自分のできることだけして会社として成長しません
成長しない=劣化です(環境が変化するから)
それはさすがにわかっていました
日本の上司は「利益どうなってるねん」だけです
具体的にするべきことなど教えてくれません
何をするか
事業や商品の方向性は明確だったのですが、それだけでは経営はできないことに気づきました
そして、現地の役割として各職能別の戦略が重要と、まずは考えました
製造戦略、調達戦略、技術、物流、人事・・・・・
いっぱいあります
まずは製造現場の改善から始めよう
職能別の戦略と言っても、海外の製造会社にはそのような戦略を考えるスタッフもいません
いろいろ情報を仕入れている中で、工場としてQCDのレベルを上げよう
まずは基本を考えました
その中で、中国の工場を担当している大先輩が「現場改善」の推進して生産性を上げているとの話を聞きました
「ヨシ、現場改善活動をして生産性向上⇒人件費削減を目指そう」
まずは、こんなところを思いついた次第です
後々「生産性を上げる」本質はもっと違うところにあることに気づきますが・・・
「生産性」の意味を狭くQCDの「C」しか考えていなかったことを後に気づきます
これは第2弾以降で
ほんで、生産性上げるなんて製造会社社やし、当たり前やわな・・・
当時の会社、とにかく数を作ればOKみたいな感じでした
ですので月次の生産台数の達成には熱意を持っていました
とにかく力づくで効率性など無視した作り方のように感じました
「これでええの???」
「もっと、やるべきことあるで~~」というのを、中国工場の先輩に学びました
それで生産性の改善に着手
製造現場の改善活動から取り組むのは、後に担当する3会社でも、同じアプローチをとりました
理由としては、
・やはり工場の基本はQCDのレベルを上げて、お客様に製品をお届けすること
・製造の改善は結果を見やすい
(変化が見えて実感でき、結果を数字にしやすい)
製造は、モノを作っている現場が変化があれば見やすいですし、生産性や不良率等数字化しやすい特徴があります
それによって、会社全体に改善を行う文化を広げやすいと考えています
まとめ
今まで記事にしてきたものづくり関する考え方をどう構築してきたかを振り返ってみました
今回は、初めてタイの工場を任され手探りから、まずは現場改善をしようと思い立ったところまです
会社の経営者として、しなければならないことはこれ以外にも当然たくさんあります
でも、正直なところ最初はいろんなトラブル(製造だけではありません)を追っかけ、その原因を探して、やっつけ仕事をすることが役割みたいなところがありました
ただ、その中で人材育成とこの生産現場の改善活動には結構エネルギー注いだつもりです
「会社をどう導こう」と明確にすることが重要と、経営の教科書には書いていますが、実践には程遠い状態でした
次回は、どのように現場改善をしていったかを書いてみます
コメント