生産性向上のための工程改善では、全体の工数(作業量)を減らしたり、ラインのバランスを良くするこを優先にしがちです
しかし、そのような活動をする前に前提とする活動として、作業者が作業に専念できる環境づくりが重要です
「作業者が作業に専念できる?」
当たり前ちやうの?と思うっている人も多いでしょうが、にできているつもりでも、できていないケースはよくあります
工場の品質、生産性を向上させたいと考えている方の参考になれば嬉しいです
工程改善の目的
まずは、工程改善目的は大きく下記二つになります
・生産性を継続的に上げ続ける=生産が増えても人を増やさず組み立てる
・不良率を継続的に下げ続ける=工程での品質の造り込み
それによって、原価が下がり、利益が増えることになります。
これを、グラフに書くと下の様になります
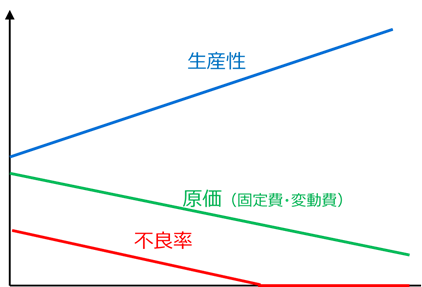
また、生産性と不良率は相関関係があり、生産性を向上すれば不良率はさがり、不良率が下がれば生産性もよくなります
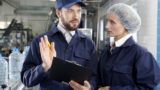
と言うことで、工程改善活動は、会社の収益向上のためには非常に重要な活動になります
この記事では、その取り組みの基本概念を話してみたいです
工程でよく発生しがちな小さなトラブル
常に現場で発生している問題でも
・マネジメント層は、常時現場にいないので、見過ごしている問題
・現場リーダーは普通過ぎて、当たり前と思っている問題
が、実は工程のロスを生んでいる原因になっています
例えば
・部品が無くなったので、作業者が部品を取りに行く
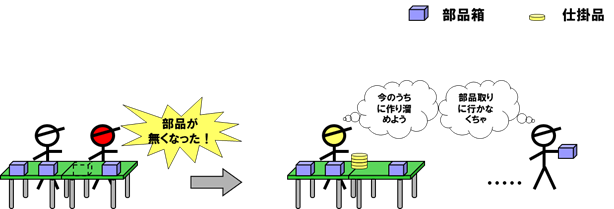
・間違えた部品が供給されてしまった
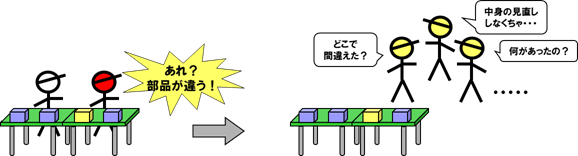
・空箱の置場が近くに無い・補材の処理に手間取る
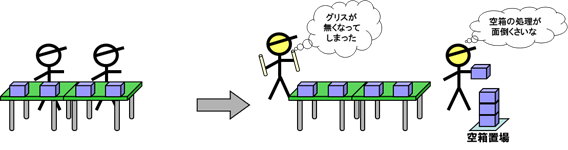
こんなトラブルが日常的に発生していないか、現場にヒアリングしてみてみてください
ただ、作業者に聞いても
「部品切れ? めった無いですよ。2週間に1回くらいかなぁ・・・」
と答える場合があります
少ないかな? っと思っても
もし、作業者が10人いれば、2週間に10回、ほぼ毎日発生してることになります
このような理由で、小さなトラブルは幹部が現場を巡視するレベルではなかなか見つかりません
ただ言えることは、上記のようなトラブルを防ぐための明確な仕組み
・部品を切らさず供給する仕組み
・部品を間違わずに供給する仕組み
・空き箱の処理の仕方の手順
が明確でない工程は、必ず、発生していると思って間違いないでしょう
工程改善の手順=工程改善の5ステップ
工程改善を行う場合、よくある間違いとして、
最初に作業者の作業工数を削減する活動を実施してしまう
ことです
作業のやり方を改善し、「60秒かかる作業を50秒にできる」みたいな改善です
これは、全く無駄とは言いませんが、工程全体の生産性を上げているかは疑問です
ライン方式の組み立てなら、一人の作業者だけの工数を減らしても、ボトルネック工程が残っていれば、ラインとしての生産性は上がりません
それに、先ほど述べたように、部品切れ等で、どこかの作業者の作業が止まったら、ライン全体が止まるので、影響が大きいです
つまり、作業者自身の作業を改善する前に、作業者の環境を整えることが重要です
そして、安定的な作業を作業者ができるようにしてから、工程のバランスや作業性を検討していくことを勧めます
私は、工程を改善する場合は下記の5ステップでするべきと考えます
①定位地:決まった「モノ(部品・仕掛品・治工具)」が、決まった「場所」にある
②表示:「モノ」にも「場所」にも表示がある
③ライン作業者が組立・加工作業に専念できる環境をつくる
「部品の安定的供給の仕組み」をつくり、部品を欠品させず、
作業者が部品供給を気にせず組み立てに専念できる環境作り
④ライン作業者が作業しやすいようにする
部品を取りやすい場所や箱に設定する、治具を工夫する等、
誰が作業しても安定的に作業ができる仕組み作り
⑤IE(インダストリアル エンジニアリング)分析:各工程の作業を分析し、課題を見つけ改善する
・バラツキの多い作業を無くす
・各作業者の負荷バランスを最適化する
①~③は工程改善するための、まずは環境整備
①②により、作業場には必要なものを必要な数だけ置かれている状態を作り
③で作業者が作業台から離れない環境を作ります
ここまでできて
④⑤で実際の作業自体の改善に入る必要があります
①~③の環境づくりができなまいまま、作業を改善しても、その効果は小さく
逆①~③をするだけでも、工程の生産性は向上します
加えて、①~③をすることによって、本来改善すべき作業の課題が見えてきます
ビデオを撮ったり、時間を図ったりする前に、現場の「見える化」=異常をわかるようにする仕組みが重要です
上記の内容を表にまとめました
参考にしてください
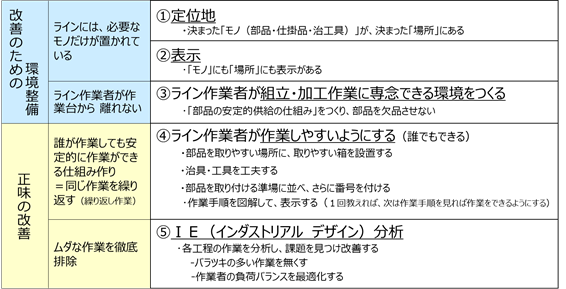
改善活動進め方のポイント
この5ステップを進めていくことで工程の改善を実現します
その時の進め方のポイントです
①1回で上手くやろうとしない
②最初からきれいに表示しない(すぐに修正できるようにしておく)
③愚直に改善サイクルを回す
④1度の改善で効果をすぐに求めない
⑤必ず現場・現物で確認する(会議室で確認しない)
要は、あれこれ考えずに、改善ポイントが見つかれば、まずは行動しましょう
行動した上で、現場を見ながら次の手を打ち、常に改善のサイクルを早く回すことです
机上であれこれ考えても、現場は何も変わりません
変えることにより、課題が見え、進歩があります
特に保守的な性質が強い人は、変えることを恐れます
しかし、今の時代、変えることのリスクより変えないリスクの方が圧倒的に高い
事業は下りのエスカレータに乗っているようなものです
じっとしていると、下がっていきます
なぜなら、周りはどんどん変化しているから
まとめ
工程改善の目的と手順についてその考え方を述べました
目的は大きく二つ
・生産性を継続的に上げ続ける=生産が増えても人を増やさず組み立てる
・不良率を継続的に下げ続ける=工程での品質の造り込み
それによって、原価が下がり、利益が増えることになります
さらにそれを進める5ステップ
作業を改善する前に作業者が作業に集中できる環境を作る
これを忘れすに取り組みましょう
コメント